Fantastic Tips About What Is The Wetting Current In A Circuit
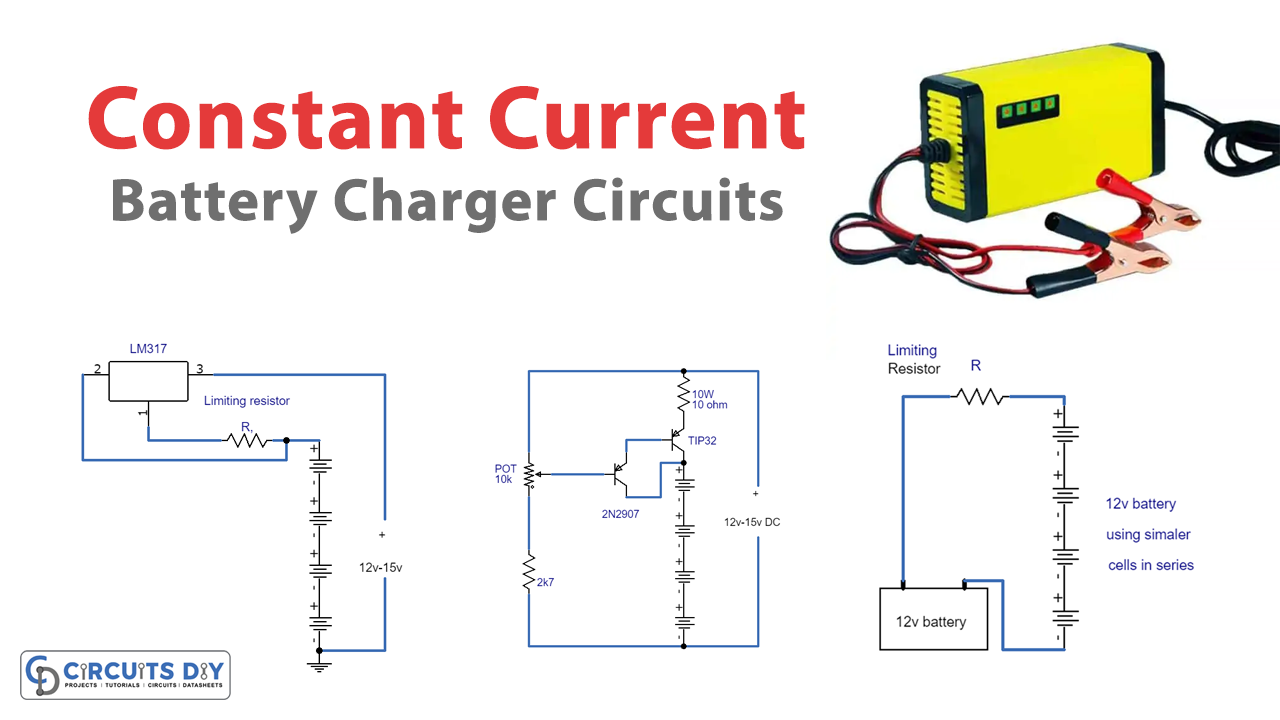
Constant Current Battery Charger Circuits
What's This "Wetting Current" Thing in a Circuit?
1. Understanding Wetting Current Basics
Ever heard of wetting current and wondered what it actually does? Well, it's not about making your circuit damp, I promise! It's actually a clever technique used to improve the reliability of electrical contacts, especially in situations where you might have very low voltages or currents flowing. Think of it as giving the contacts a little nudge to make sure they're properly connected, even when things are a bit... lazy.
So, basically, a wetting current is a minimum current that's needed to break down any surface films or oxidation that might have formed on the contacts of a switch or relay. These films can act like insulators, preventing a good electrical connection. Applying a wetting current punches through these films, ensuring that the circuit closes properly and you get a reliable signal. Without it, you might experience intermittent connections, which can be a real headache, especially in sensitive applications.
Think about it like this: imagine trying to start a car that's been sitting unused for a long time. Sometimes, the battery terminals get a little corroded, right? You might have to wiggle the connection a bit to get it to start. A wetting current is kind of like that wiggle, but done automatically within the circuit. It's a proactive measure to keep things running smoothly.
Wetting current isn't a newfangled invention. Its been around for ages, quietly doing its job in various electronic systems. It is especially beneficial in applications that require reliability, and where contact resistance might cause problems, such as in industrial control systems or medical devices. These applications are more often subject to failures, and it is important that equipment reliability is at the highest standards possible.

Voltagecurrent Characteristics In The Wet ESP. Download Scientific
Why is Wetting Current So Important?
2. The Impact of Contact Resistance
Okay, so we know it cleans up contacts, but why is that so crucial? The main culprit here is contact resistance. Over time, even the cleanest metallic surfaces can develop thin layers of oxidation or other contaminants. These layers add resistance to the circuit, making it harder for current to flow and potentially causing all sorts of problems. And in some systems, a false trigger could be detrimental.
Now, in high-voltage or high-current circuits, this added resistance might not be a big deal. The voltage is high enough to punch through the film and establish a good connection. But when you're dealing with low-voltage or low-current circuits, those thin films can become a significant barrier, potentially preventing the circuit from working at all. This is where wetting current becomes really handy. By ensuring a certain level of current flows, it overcomes the contact resistance, thus improving the reliability of the circuit.
Imagine a delicate sensor circuit designed to detect a tiny change in temperature. If the contacts in the circuit are unreliable due to oxidation, the sensor might not be able to register the change accurately. This could lead to inaccurate readings or even system failure. By implementing a wetting current, you can ensure that the contacts remain clean and reliable, so the sensor can do its job without any hiccups.
Furthermore, problems related to oxidation, and film layering can increase over time, especially in humid environments. This is a significant issue in industrial plants where machines are often operating in challenging conditions. This ensures that there are no false triggers, or other potentially damaging faults from happening.
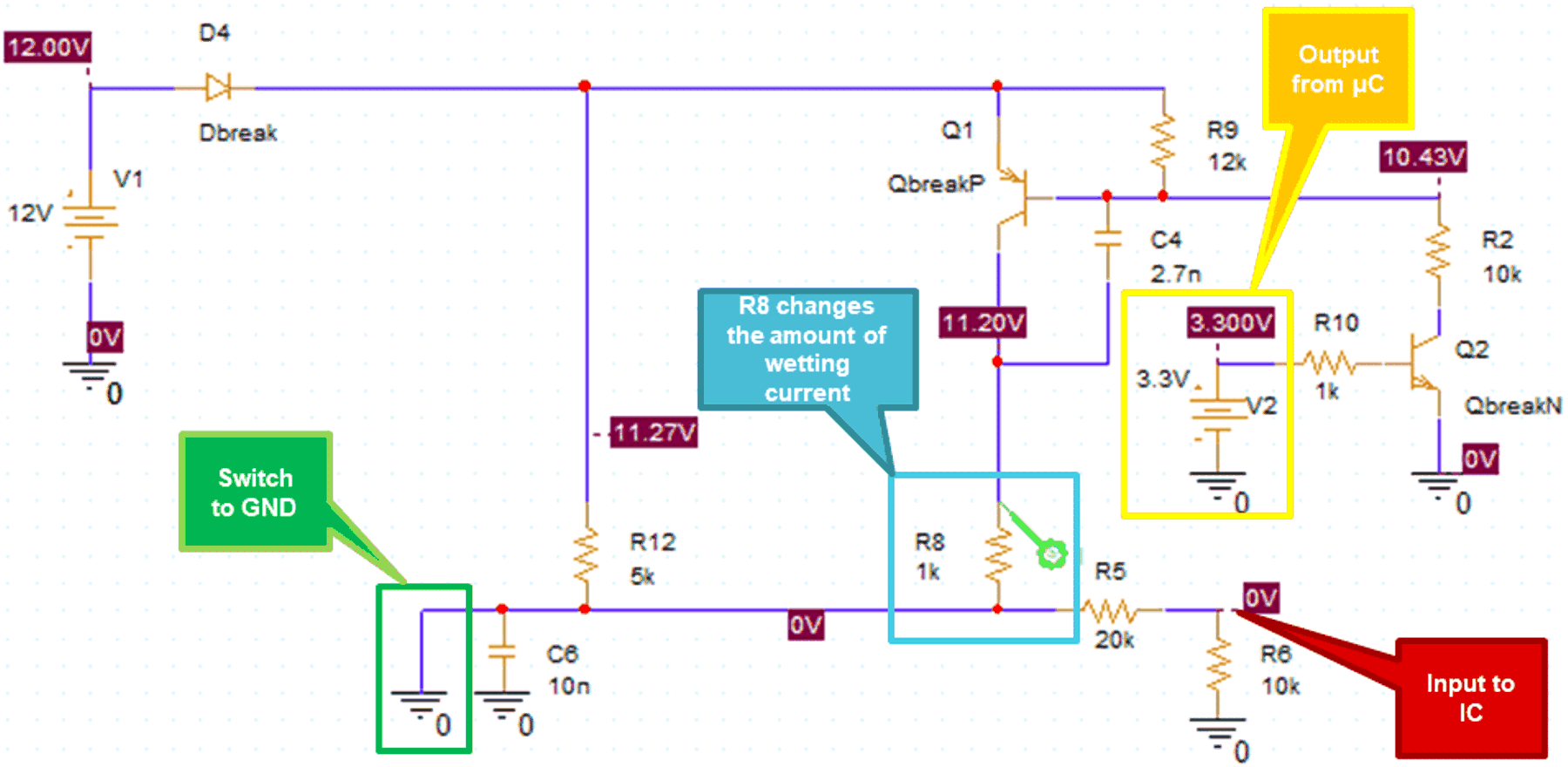
SLLA606 Application Brief
Where Do We Use Wetting Current?
3. Applications Across Industries
You'll find wetting current being used in a surprising number of places, especially where reliability is paramount. One common application is in industrial control systems, where sensors and switches constantly monitor and control various processes. These systems often rely on low-voltage signals, so maintaining reliable contacts is crucial for accurate operation.
Another important area is in medical devices. In these devices, even a small malfunction can have serious consequences, so ensuring reliable connections is a top priority. Wetting current can help to prevent intermittent connections and ensure that medical devices operate smoothly and accurately. It would be pretty scary if your medical device failed when you needed it most.
It's also used in things like security systems and fire alarms. Imagine if a smoke detector failed to trigger because of oxidized contacts! Not good. Wetting current helps to ensure that these critical systems work when they're needed most, potentially saving lives and property.
Don't forget about automotive electronics, too! Modern cars are packed with sensors and electronic control units (ECUs) that rely on reliable electrical connections. Wetting current can help to improve the reliability of these systems, leading to better performance and safety on the road. From the airbags to the antilock brakes, you're always going to want the highest quality systems to keep you safe.
Need Help Clipping High Power AC Current For Both Top And Bottom Of
How Much Wetting Current Do We Need?
4. Finding the Right Balance
So, how do you know how much wetting current to use? Well, it depends on a few factors, including the type of contact material, the operating environment, and the expected lifespan of the device. Too little current, and you might not effectively break down the surface films. Too much current, and you could potentially damage the contacts or reduce their lifespan.
Typically, the wetting current is specified by the manufacturer of the switch or relay. It's usually a relatively small current, often in the range of a few milliamperes. The key is to find a balance between ensuring reliable contact and avoiding any damage or premature wear. Using the specification of the manufacturer, ensure that you are getting the proper equipment or products that will not be subject to early failure.
There are also some general guidelines you can follow. For example, gold-plated contacts generally require less wetting current than tin-plated contacts, as gold is less prone to oxidation. Also, if the device is operating in a harsh environment with high humidity or temperature, you might need to increase the wetting current to compensate for the increased oxidation rate.
It's also worth noting that some circuits use a technique called "cold switching," where the contacts are closed before any voltage is applied. This can help to reduce the amount of wetting current needed, as there's less chance of arcing or contact wear. Cold switching is also used when high inrush currents may cause problems, as well as when the circuit is very fragile, to ensure that there is the least chance of faults occurring.

Illustration Showing How Different Surface Wetting States That Are
Wetting Current
5. Ensuring Reliable Circuits
So, there you have it — a whirlwind tour of wetting current. It's not the flashiest topic in electronics, but it's a really important one, especially when it comes to ensuring reliable and consistent performance in low-voltage or low-current circuits. By breaking down surface films and oxidation on contacts, it helps to prevent intermittent connections and ensures that signals are transmitted accurately.
Whether you're designing industrial control systems, medical devices, or just trying to improve the reliability of your home automation projects, wetting current is a technique that's worth considering. It might seem like a small detail, but it can make a big difference in the overall performance and reliability of your circuits. It is the little things that matter, so always keep this in the back of your mind when designing your equipment. Think of it like a secret weapon to combat oxidation!
So, next time you're troubleshooting a circuit that's acting up, don't forget to check the contacts. A little wetting current might be all you need to get things working properly again. And who knows, you might even impress your friends with your newfound knowledge of this little-known but essential aspect of electronics. Consider this knowledge in your next design as well, as it might provide the difference needed in having a stable and reliable machine.
In a world where everything is becoming increasingly reliant on electronics, ensuring the reliability of our circuits is more important than ever. Wetting current is just one tool in the arsenal, but it's a valuable one that can help to keep our devices running smoothly and reliably for years to come. Remember, reliability is key, and wetting current can help you achieve it!
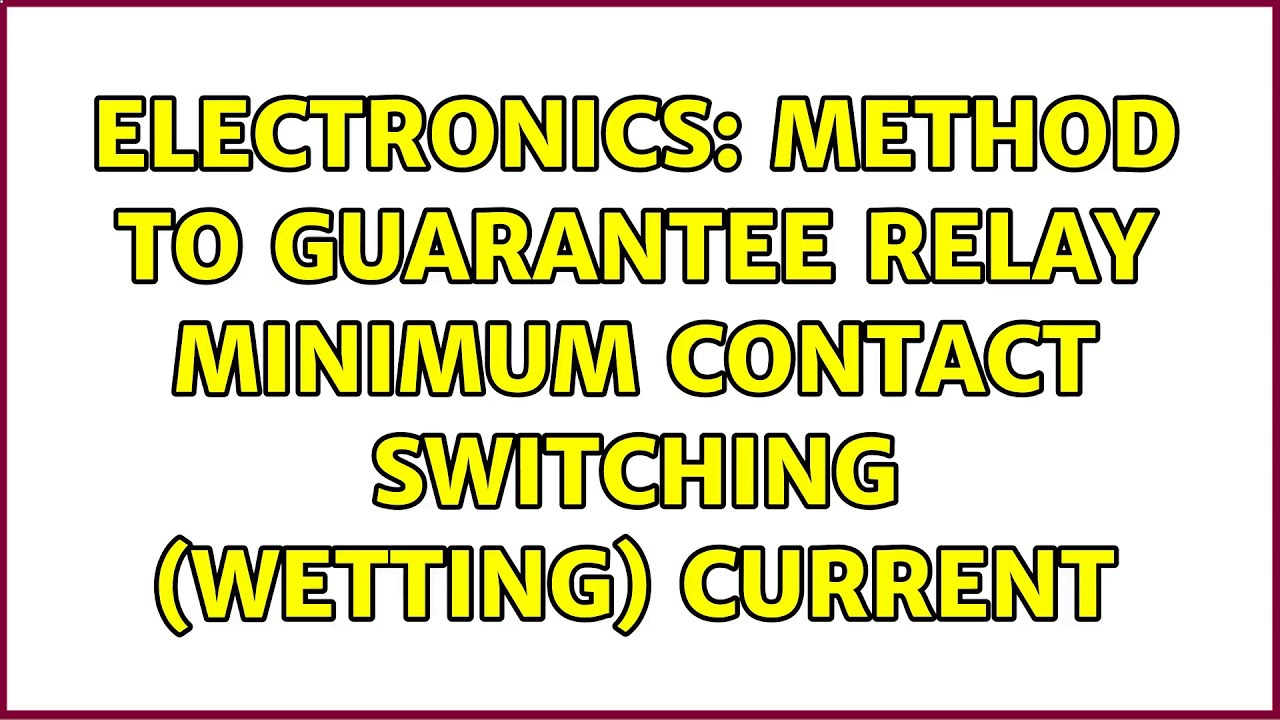
Electronics Method To Guarantee Relay Minimum Contact Switching
Frequently Asked Questions (FAQs)
6. Answers to Common Wetting Current Queries
Got more questions about wetting current? No problem! Here are a few common questions and their answers to help you solidify your understanding:
Q: Can I use too much wetting current?A: Absolutely! While a wetting current is designed to clean contacts, an excessive amount can cause damage, like overheating and accelerated wear. Always adhere to the manufacturers specifications for the components you are using. A good design should never go over the specifications as it can cause damage, and possibly injuries.
Q: Does wetting current apply to all types of switches and relays?A: Not necessarily. Its most relevant for switches and relays dealing with low voltages and currents. High-power circuits often have enough inherent energy to break through any surface films without the need for an additional wetting current. So, consider the application before applying these designs.
Q: How can I tell if my circuit needs a wetting current?A: If you are experiencing intermittent or unreliable connections in a low-voltage or low-current circuit, especially in environments prone to oxidation, a wetting current might be beneficial. Also, if there are multiple false triggers, then this might be an option to implement in your machines.
Q: Are there alternatives to using a wetting current?A: Yes, contact materials with low oxidation properties like gold can be used to reduce the need for wetting current. Also, using sealed relays or switches can protect the contacts from environmental contamination. Remember to find a cost-effective solution that is beneficial to your designs.