Perfect Info About How Much Weight Can Tie Wire Hold
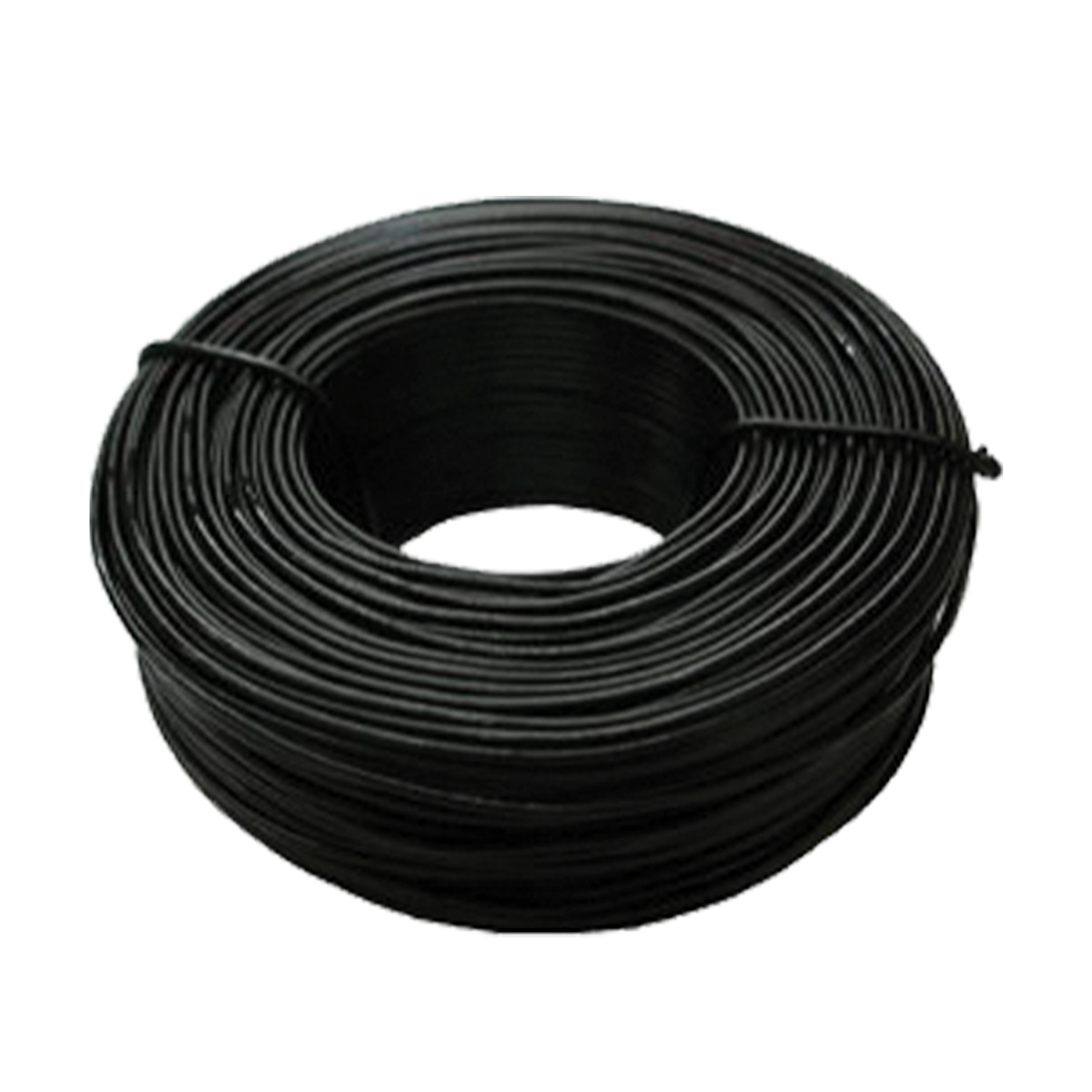
Tie Wire CanCell Industries Inc.
Tie Wire Strength
1. Understanding Tie Wire Load Capacity
Ever wondered about those unassuming little strands of tie wire holding things together on construction sites? They might seem insignificant, but they play a crucial role. The real question is: how much weight can tie wire hold? It's not as simple as a single number, because several factors come into play. Think of it like asking how fast a car can go; it depends on the engine, the tires, and who's behind the wheel!
First off, the gauge (or thickness) of the wire is a big deal. Thicker wire, logically, can handle more weight. But its not just about thickness; the type of steel used also matters. Some steels are inherently stronger than others. Then there's the way the wire is tied; a sloppy tie will significantly reduce its holding power compared to a properly twisted and secured one. Improper techniques could lead to slippage or even breakage under stress, rendering the wire ineffective when you most need it.
Think of it this way: imagine trying to lift a heavy box with a thin piece of string versus a thicker rope. The rope will obviously win. Tie wire is similar. Lighter-gauge wire might be fine for securing rebar for a small concrete pour, but you'd need something much beefier for suspending heavy ductwork. Always consider the specific application and the anticipated load before choosing your tie wire.
Finally, and this is super important, always factor in a safety margin. Just because a tie wire can theoretically hold a certain weight doesn't mean you should push it to its absolute limit. Unexpected stresses, vibrations, or even just the passage of time can weaken the wire. A good rule of thumb is to only use the wire to about 25% of its stated maximun strength.

Galvanized Wire Sack Ties/ Bag Loop Rebar Tie 6
Factors Affecting Tie Wire Load Capacity
2. Digging Deeper into Wire Strength
Okay, so we've established that tie wire strength isn't a one-size-fits-all kind of deal. Let's break down those influential factors in more detail. The gauge of the tie wire is where you should start. Tie wire, which is a noun, is usually measured in gauge, with lower numbers indicating thicker wire. For example, 16-gauge wire is thinner than 12-gauge wire. Thicker wire offers more cross-sectional area to resist tension, resulting in greater load-bearing capacity. Selecting the correct gauge can be the difference between success and failure in your project.
Material composition is another key consideration. Most tie wire is made from steel, but different alloys and treatments can significantly affect its strength and durability. For instance, galvanized steel provides corrosion resistance, making it ideal for outdoor applications where the wire is exposed to the elements. Annealed steel, on the other hand, is softer and more pliable, making it easier to work with but potentially less strong than high-carbon steel. Consider your environmental conditions, and what sort of resistance to the elements you need.
The tying technique is often overlooked but has a massive impact. A loose or poorly executed tie can dramatically reduce the wire's holding power. Properly twisted and secured ties distribute the load more evenly, maximizing the wire's strength. Always use appropriate tying tools and techniques to ensure a secure and reliable connection. This is not the place to get creative. Follow the instructions that come with the tools and wire to avoid any nasty surprises.
Environmental factors can also play a role. Extreme temperatures, humidity, and exposure to corrosive substances can degrade the wire over time, reducing its strength. Regularly inspect tie wires in harsh environments and replace them as needed to maintain the integrity of your structures. This is particularly crucial for applications where safety is paramount, such as scaffolding or temporary supports.
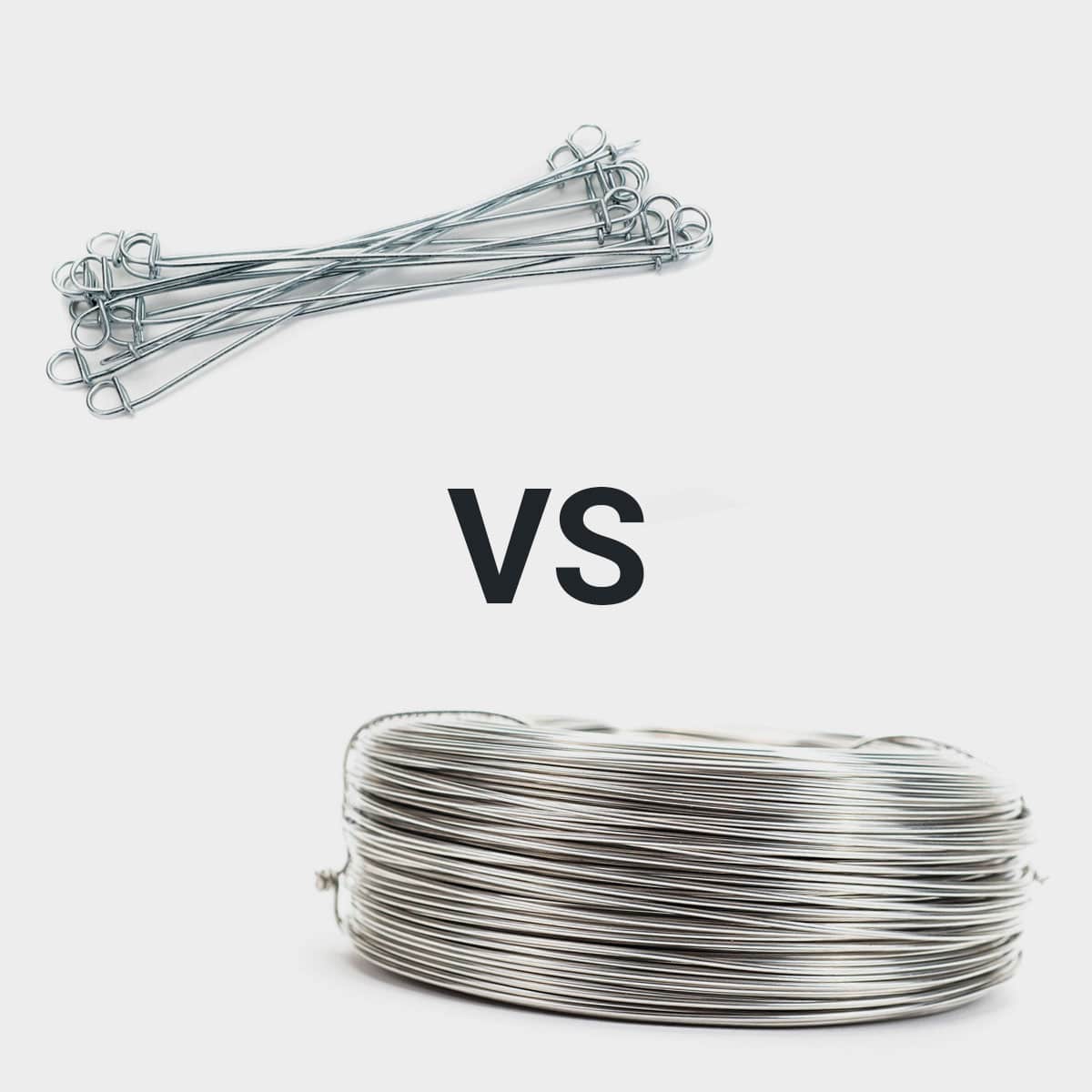
What Is The Difference Between Tie Wire And Ties? Rebar
Common Tie Wire Gauges and Their Approximate Weight Limits
3. A Practical Guide to Choosing the Right Wire
Alright, let's get practical. While precise weight limits vary depending on the manufacturer and specific steel grade, here's a general guideline for common tie wire gauges. Keep in mind this is just a rough estimate, always check the manufacturer's specifications for the actual weight limit of the specific wire you're using. When in doubt, it's always better to over-engineer than under-engineer. Err on the side of caution and choose a wire that's stronger than you think you need.
Typically, 16-gauge tie wire is used for lighter applications, such as securing rebar in concrete slabs or hanging lightweight fixtures. It generally has a tensile strength of around 200-300 pounds, but its safe working load is much lower, maybe around 50-75 pounds. The important part to remember is that it should not be used for supporting any significant weight alone. Think of it more as a temporary fastening than a permanent support.
Moving up to 14-gauge tie wire, you get a noticeable increase in strength. This gauge is often used for tying rebar in walls and columns, as well as securing heavier items. Its tensile strength can range from 300-400 pounds, with a safe working load of approximately 75-100 pounds. This offers a bit more security but still requires caution when supporting substantial weights. This is where a little bit of research and knowing your limitations is key.
For heavier-duty applications, such as securing precast concrete panels or supporting temporary structures, 12-gauge or even 10-gauge tie wire may be necessary. These thicker gauges can handle significantly higher loads, with tensile strengths exceeding 400 pounds and safe working loads ranging from 100 pounds upwards. However, always consult with a structural engineer or experienced professional to determine the appropriate gauge and tying technique for your specific project. Don't guess. It's not worth the risk.
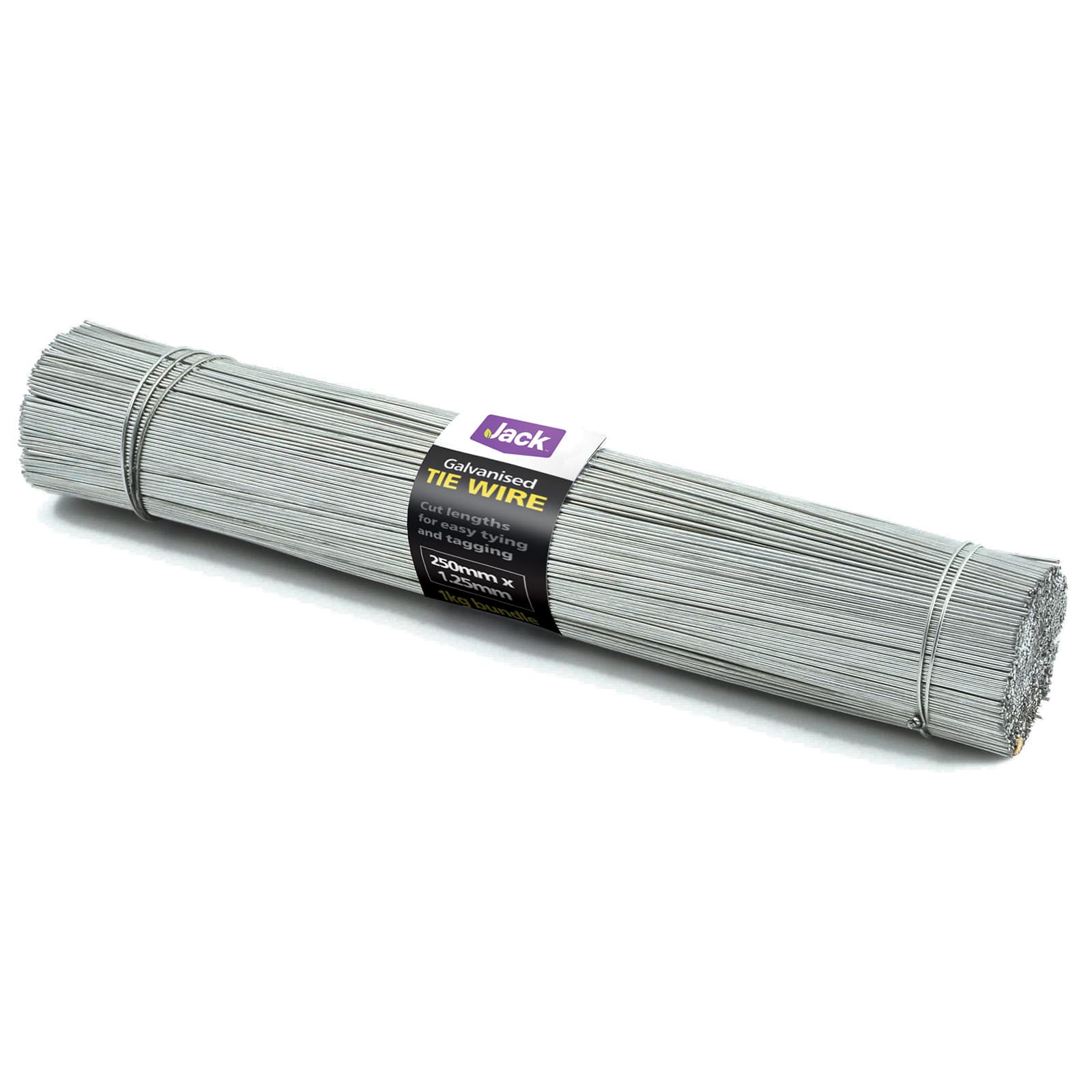
Cut Length Tie Wire Jack
Ensuring Safety
4. Tips for Reliable and Secure Connections
Safety should always be your top priority when working with tie wire. It might seem like a small component, but a failure can have serious consequences. Always wear appropriate personal protective equipment (PPE), including gloves and eye protection, to prevent injuries from sharp wire ends or flying debris. Tie wire, when cut, can become a projectile. Treat it with the respect it deserves.
Before using any tie wire, inspect it carefully for any signs of damage, such as rust, kinks, or breaks. Damaged wire can be significantly weaker and more prone to failure. Discard any damaged wire immediately and never attempt to use it. These signs indicate a loss of the wire's structural integrity, and is a clear indication it should be retired.
Use the correct tying tools and techniques for the specific application. Proper tying tools ensure a tight, secure connection and reduce the risk of slippage or breakage. Over-tightening can also damage the wire, so use the tool within the manufacturer's guidelines. Incorrect techniques could lead to a weak, unreliable, and ultimately useless connection.
Regularly inspect tie wire connections, especially in applications where safety is critical. Look for any signs of loosening, corrosion, or damage. Replace any compromised connections immediately. Proactive inspection and maintenance can prevent potential accidents and ensure the long-term integrity of your structures. Its a small price to pay for peace of mind.
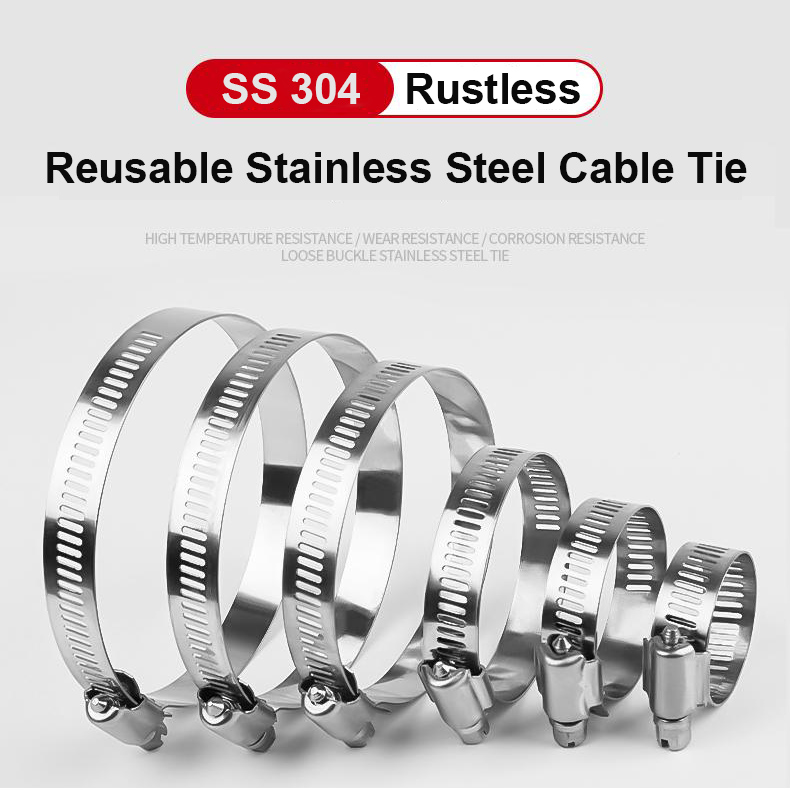
Real-World Examples and Applications
5. Where You'll Find Tie Wire in Action
Tie wire is incredibly versatile and finds its way into countless applications. Construction sites are probably the most common place you'll spot it, securing rebar in concrete structures, holding scaffolding together, and bundling materials for transport. The next time you drive by a construction site, take a moment to appreciate the humble tie wire doing its job, unseen but essential.
Agriculture is another area where tie wire shines. Farmers use it for fencing, tying plants to supports, and even repairing equipment. Its affordability and ease of use make it a valuable tool for various tasks around the farm. Think of the endless rows of crops supported by simple tie wire — a testament to its practicality.
Even in artistic endeavors, tie wire has a place. Sculptors and crafters use it to create wire sculptures, jewelry, and other decorative items. Its pliability and strength make it an ideal material for shaping intricate designs. Artists are always finding new and innovative ways to utilize its unique properties.
In emergency situations, tie wire can be a lifesaver. It can be used for temporary repairs, securing makeshift shelters, or even creating improvised tools. Its versatility and availability make it a valuable asset in survival situations. Knowing how to use it effectively could make all the difference.
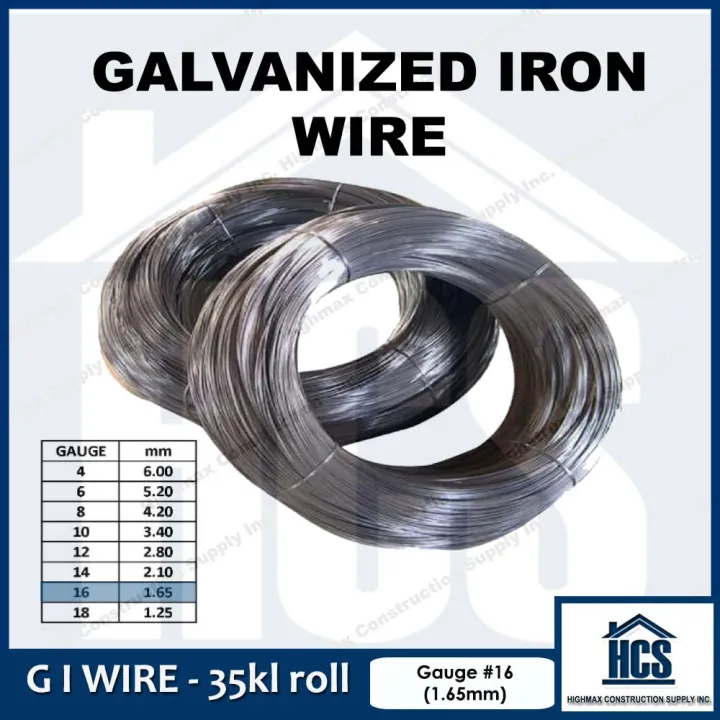
Galvanized Iron Wire GI Gauge No. 16 (35kgs) HotDipped Alambre
FAQ about Tie Wire
6. Your Questions Answered
Q: What happens if I use tie wire that's too thin for the load?A: Using tie wire that's too thin can lead to catastrophic failure. The wire could snap under the load, causing whatever it's holding to collapse or fall. This could result in serious injury or property damage. Always choose the appropriate gauge and type of tie wire for your specific application.
Q: How does corrosion affect tie wire strength?A: Corrosion weakens tie wire by reducing its cross-sectional area and compromising its structural integrity. Rust eats away at the steel, making it more brittle and prone to failure. Galvanized or epoxy-coated tie wire offers better corrosion resistance, but even these protective coatings can degrade over time. Regularly inspect tie wire in corrosive environments and replace it as needed.
Q: Can I reuse tie wire?A: It's generally not recommended to reuse tie wire, especially in critical applications. Once tie wire has been subjected to stress, it can become weakened or damaged, even if it doesn't look like it. Reusing tie wire increases the risk of failure and compromises safety. Fresh wire is worth the cost for critical applications, its cheap insurance for your job.
Q: Where can I find the manufacturer's specifications for tie wire?A: The manufacturer's specifications for tie wire are usually printed on the packaging or available on their website. Look for information on tensile strength, yield strength, safe working load, and recommended applications. Always follow the manufacturer's recommendations to ensure safe and reliable performance.